
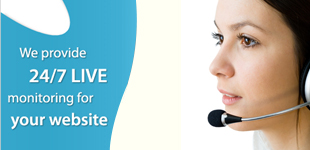
- : 0086-371-86151627 0086-371-86151827
- : 0086-371-86011881
- : [email protected]
- : [email protected]
- : bebonchina

- Boiler steels
- High carbon steel
- High Yield steel
- steel for welded tubes
- General construction steel
- steel with Cr.,Mo.,Cr-Mo
- Steel for large diameter pipes
- Simple pressure vessels steel
- Steel for gas cylinders and gas vessels
- General purpose structural steels
- Steel for boilers and pressure vessels
- steel resistant to atmospherical corrosion
- Carbon steel and low alloy steel
- Fine-grain structural steels,normalised rolled
- weldable normalized fine grained pressure vessel steels
Welding method of SG365 steel
There are many welding methods for gas cylinders, commonly used are electrode arc welding, submerged arc welding, argon tungsten arc welding, and melt inert-gas welding. This article mainly writes about the latter two welding methods.
The characteristic of argon tungsten arc welding is that the heat is concentrated, which is conducive to reducing the width of the heat-affected zone, in order to improve the mechanical properties and crack resistance of SG365 steel. In addition, although the welding efficiency of argon tungsten arc welding is low, its hydrogen content in the weld is much lower than that of submerged arc welding and electrode arc welding, which can effectively prevent the cracks of SG365 steel due to delay caused by hydrogen.
Melt inert-gas welding (MIG) retains the advantages of extremely low hydrogen content and high welding efficiency of the other three arc welding technologies in the weld seam, and improves arc stability of SG365 steel while reducing arc radiation intensity. After the welding is completed, the air tightness test must be carried out. The specific operation process of welding for SG365 steel is to check whether there is any air leakage at the weld of the drainage tube after closing the valve on the drainage tube tightly.