
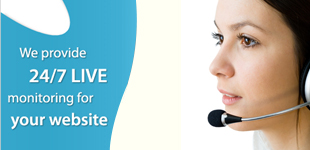
- : 0086-371-86151627 0086-371-86151827
- : 0086-371-86011881
- : [email protected]
- : [email protected]
- : bebonchina

- Boiler steels
- High carbon steel
- High Yield steel
- steel for welded tubes
- General construction steel
- steel with Cr.,Mo.,Cr-Mo
- Steel for large diameter pipes
- Simple pressure vessels steel
- Steel for gas cylinders and gas vessels
- General purpose structural steels
- Steel for boilers and pressure vessels
- steel resistant to atmospherical corrosion
- Carbon steel and low alloy steel
- Fine-grain structural steels,normalised rolled
- weldable normalized fine grained pressure vessel steels
Surfacing process of NM600 wear plate
The alloy layer of the NM600 steel has high wear resistance, and the service life of the parts after surfacing is relatively long, which will increase by about eight times compared with the traditional service life.
NM600 wear-resistant plates generally use flux-cored welding wire for surfacing welding. The thermal efficiency of open arc surfacing welding is similar to that of submerged arc surfacing welding, but the former also has its own advantages, because NM600 wear-resistant plates do not need rust removal process and can be directly stacked on it. There is no need to add other flux during surfacing, the whole process is relatively simple, and there is no need to clean up a lot of welding slag after surfacing of NM600 wear-resistant.
A small amount of alloy powder materials are used in NM600 wear-resistant plate surfacing. These materials can ensure the high hardness of NM600 wear-resistant plate and improve the wear resistance of the substrate. After welding, the surface is smooth and the shape is also good. It is of great value for practical application.
The surfacing process of NM600 wear-resistant plate has requirements for current, voltage and welding speed. These factors determine the final surfacing effect of NM600 wear-resistant plate, and the diluted components also have a decisive influence on the microstructure and properties of the welding layer. Surfacing of NM600 wear-resistant is divided into straight-forward welding and step-by-step welding, and the specific welding form should be set according to the needs.