
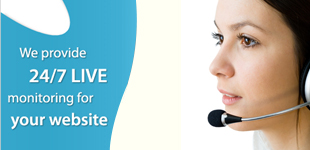
- : 0086-371-86151627 0086-371-86151827
- : 0086-371-86011881
- : [email protected]
- : [email protected]
- : bebonchina

- Boiler steels
- High carbon steel
- High Yield steel
- steel for welded tubes
- General construction steel
- steel with Cr.,Mo.,Cr-Mo
- Steel for large diameter pipes
- Simple pressure vessels steel
- Steel for gas cylinders and gas vessels
- General purpose structural steels
- Steel for boilers and pressure vessels
- steel resistant to atmospherical corrosion
- Carbon steel and low alloy steel
- Fine-grain structural steels,normalised rolled
- weldable normalized fine grained pressure vessel steels
Main Points of Production for 50CrMo4 Steel
Casting Technology
There are two mainstream methods for 50CrMo4 smelting and casting, one is electric arc furnace smelting, secondary refining and vacuum degassing, and the other is converter steelmaking and continuous casting technology adopted by large steel mills.
The difference is that electric arc furnace steelmaking is suitable for small batch production, and the composition of molten steel is greatly affected by scrap steel. Converter steelmaking is suitable for mass production, and the purity of molten steel is high. Compared with electric arc furnace steelmaking, the smelting cycle is shorter and the power consumption is lower.
Thermal processing
Corresponding to the smelting and casting process, the 50CrMo4 steel ingot produced by EAL+LF+VD is mainly used for hot forging, including free forging and die forging.
The 50CrMo4 steel billet produced by the converter + continuous casting process is usually used as a hot-rolled product, and the production efficiency is extremely high.
A final note is that they can be applied to each other, but must match the size of the billet to ensure adequate compression.
Preliminary heat treatment process selection
For 50CrMo4 steel, after hot rolling or hot forging, it can usually be delivered without heat treatment. But sometimes considering the machinability of the material, 50CrMo4 steel is usually selected for softening annealing treatment.
Choosing 50CrMo4 for normalizing is often to improve processing performance, eliminate internal stress, and prepare a good metallographic structure for final heat treatment.