
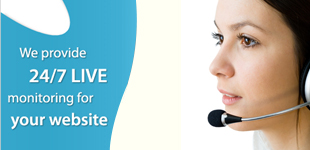
- : 0086-371-86151627 0086-371-86151827
- : 0086-371-86011881
- : [email protected]
- : [email protected]
- : bebonchina

- Boiler steels
- High carbon steel
- High Yield steel
- steel for welded tubes
- General construction steel
- steel with Cr.,Mo.,Cr-Mo
- Steel for large diameter pipes
- Simple pressure vessels steel
- Steel for gas cylinders and gas vessels
- General purpose structural steels
- Steel for boilers and pressure vessels
- steel resistant to atmospherical corrosion
- Carbon steel and low alloy steel
- Fine-grain structural steels,normalised rolled
- weldable normalized fine grained pressure vessel steels
Internal Defects of Welding for Q345R Steel
Common welding defects of Q345R steel include appearance defects and internal defects. Appearance defects include undercut, depression, surface pores, cold cracks, etc.; internal defects include hot cracks, cold cracks, internal pores, slag inclusions, incomplete penetration, etc.
1. Cold crack
Q345R steel is a special steel for low-alloy pressure vessels, its carbon equivalent is about 0.4%, and its welding performance is excellent. Except for welding conditions such as large-thickness steel plates and low ambient temperature, preheating and strict control of heat input are generally not required to control welding cold cracks, so Q345R steel is not easy to produce welding cold cracks under normal welding conditions.
2. Hot crack
Q345R steel because of its high Mn content. The ratio of Mn/S can meet the requirements of preventing crystallization cracks, and has a good ability to resist thermal cracks. When the chemical composition of the base metal is normal, and the welding materials and welding parameters are selected correctly, thermal cracks will generally not occur.
3. Stomata
Basic electrodes should be dried at 350-400℃ for 1.5-2.5h according to regulations, and acidic electrodes should be dried at 200-250℃ for 1-1.5h according to regulations. To ensure that the welding place is kept clean, during the process of welding Q345R steel, it should be noted that the welding current should be appropriate, and the speed should not be too fast when welding Q345R steel, and the gas in the molten pool should be completely released. Once there is any remaining gas, it may affect the welding quality.
4. Weld slag inclusions
The occurrence of welding cracks is mainly caused by the following factors: the groove is not clean, or the size is not suitable; when performing multi-layer welding, the slag is not cleaned thoroughly; the heat dissipation speed of the weld is too fast; the electrode powder used The composition of the skin is wrong, and the slag is difficult to float.
5. Incomplete penetration
The reasons for incomplete penetration mainly include: the size of the groove and the gap is not suitable; the eccentricity of the electrode is too large; the root of the electrode and the cleaning between the layers are not properly cleaned. The most basic way to prevent lack of penetration is to use a larger line of energy when welding.