
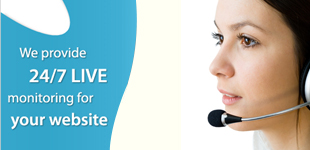
- : 0086-371-86151627 0086-371-86151827
- : 0086-371-86011881
- : [email protected]
- : [email protected]
- : bebonchina

- Boiler steels
- High carbon steel
- High Yield steel
- steel for welded tubes
- General construction steel
- steel with Cr.,Mo.,Cr-Mo
- Steel for large diameter pipes
- Simple pressure vessels steel
- Steel for gas cylinders and gas vessels
- General purpose structural steels
- Steel for boilers and pressure vessels
- steel resistant to atmospherical corrosion
- Carbon steel and low alloy steel
- Fine-grain structural steels,normalised rolled
- weldable normalized fine grained pressure vessel steels
Influence of gas in 42CrMo4 steel
Gas in steel is a general term for gases such as oxygen, nitrogen, and hydrogen in the medium absorbed by steel during smelting, welding, or chemical and electrochemical reactions on the steel surface. The gas in the steel has adverse effects on the performance of 42CrMo4 steel, and its content should be strictly controlled.
Oxygen in steel
Steelmaking itself is an oxidation process. Although deoxidizers such as ferromanganese, ferrosilicon, and aluminum are added in the later stage of steelmaking, part of the oxygen is still dissolved in 42CrMo4 steel. Oxygen generally dissolves in ferrite, or forms oxides such as FeO, SiO2, MnO, Al2O3 (that is, non-metallic inclusions in steel), which reduces the tensile strength, plasticity and toughness of 42CrMo4 steel. Especially when inclusions exist, the fatigue strength of 42CrMo4 steel decreases, and the hot and cold workability becomes poor. Therefore, oxygen control technologies such as VD deoxidation must be strictly adopted to keep the oxygen content of 42CrMo4 steel below 20ppm or even lower.
Nitrogen in steel
During steelmaking, molten steel absorbs nitrogen from the air. Part dissolves in ferrite, and part becomes non-metallic inclusions. When 42CrMo4 steel does not contain Al, Ti, Zr and other elements, most of the nitrogen and iron form needle-like compounds Fe4N. Although the presence of Fe4N increases the strength of 42CrMo4 steel, it greatly reduces its plasticity and toughness. By preventing LF nitrogen absorption technology and increasing VD denitrification rate, these two methods can effectively reduce nitrogen content, and can effectively control nitrogen content below 90ppm.
Hydrogen in steel
The solubility of hydrogen in 42CrMo4 steel decreases significantly with the decrease of temperature. When hydrogen exists in the atomic state, it dissolves into the interstices of the iron. When the dissolved hydrogen in the steel exceeds 3 milliliters per 100 grams, it will exist in a molecular state, and hair-like cracks will appear on the internal cross-section of 42CrMo4 steel ingot or forging, which is called cracking. They look like oval, silvery-white spots and are therefore also called white spots. White spots make steel hydrogen embrittlement. Low carbon steel is not easy to form white spots, but medium carbon alloy steel, especially medium carbon nickel chromium molybdenum steel is the most sensitive to hydrogen embrittlement. For 42CrMo4 steel, it is also easy to form white spots, causing the material to crack.
VD vacuum degassing technology can effectively remove hydrogen. In order to avoid embrittlement, 42CrMo4 steel can also be annealed at about 650 ° C to diffuse hydrogen from the steel, eliminate supersaturated state, and achieve the purpose of hydrogen removal. Generally, the hydrogen content can be controlled below 2.0ppm