
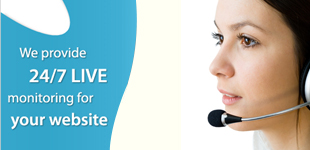
- : 0086-371-86151627 0086-371-86151827
- : 0086-371-86011881
- : [email protected]
- : [email protected]
- : bebonchina

- Boiler steels
- High carbon steel
- High Yield steel
- steel for welded tubes
- General construction steel
- steel with Cr.,Mo.,Cr-Mo
- Steel for large diameter pipes
- Simple pressure vessels steel
- Steel for gas cylinders and gas vessels
- General purpose structural steels
- Steel for boilers and pressure vessels
- steel resistant to atmospherical corrosion
- Carbon steel and low alloy steel
- Fine-grain structural steels,normalised rolled
- weldable normalized fine grained pressure vessel steels
How to avoid bursting of wear-resistant plate during cutting
Due to its high hardness, the wear-resistant plate is one of the commonly used raw materials in the manufacturing process of engineering machinery and mining equipment. In the process of selling the wear-resistant plate, sometimes customers will report that the wear-resistant plate is cracked in the cutting process, especially when the temperature is relatively low in winter. But the performance of all parties of the wear-resistant plate purchased completely meets the standard requirements when leaving the factory.
Based on this situation, the explanation given by the steel factory is as follows: flame cutting process of wear-resistant plate (except water knife cutting): please follow the following minimum preheating temperature for flame cutting of finished plate:
The minimum preheating temperature is 100 ℃ when the plate thickness is less than 30mm,
The plate thickness is 30 ~ 50mm, and the minimum preheating temperature is 150 ℃,
The plate thickness is 50 ~ 80mm, and the minimum preheating temperature is 170 ℃,
If the plate thickness is greater than 80mm, the preheating temperature shall be appropriately increased as appropriate, and the maximum preheating temperature of all thicknesses shall not be greater than 300 ℃.
Customers should adopt preheating and slow cooling methods when cutting wear-resistant plates with heat source, so as to prevent the problem of delayed crack caused by flame cutting.