
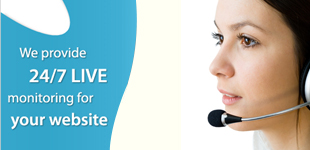
- : 0086-371-86151627 0086-371-86151827
- : 0086-371-86011881
- : [email protected]
- : [email protected]
- : bebonchina

- Boiler steels
- High carbon steel
- High Yield steel
- steel for welded tubes
- General construction steel
- steel with Cr.,Mo.,Cr-Mo
- Steel for large diameter pipes
- Simple pressure vessels steel
- Steel for gas cylinders and gas vessels
- General purpose structural steels
- Steel for boilers and pressure vessels
- steel resistant to atmospherical corrosion
- Carbon steel and low alloy steel
- Fine-grain structural steels,normalised rolled
- weldable normalized fine grained pressure vessel steels
Hot rolling process of SPA-C steel
The SPA-C steel billet is hot delivered and hot loaded to a 1500mm hot continuous rolling mill for rolling. SPA-C steel has a high Cu content, and "copper embrittlement" is prone to occur during the heating process, that is, the surface of the slab is prone to cracks during heating, resulting in edge cracking of the finished plate. Therefore, the heating adheres to the principle of "high temperature and fast burning" to ensure that the slab is heated in a reducing or neutral atmosphere, accelerate the heating rate during heating, increase the temperature of the heating section, prevent excessive oxidation, and reduce the enrichment of Cu at the grain boundary and the surface of the slab , to avoid edge cracking of SPA-C steel during rolling, and to properly reduce the soaking temperature. The temperature of the slab out of the furnace is: 1160-1210°C, and the heating time is not less than 80min.
The material of SPA-C steel is relatively hard, and the specification of rolling is usually thinner. During the rolling process, the rolling force and rolling current of the finishing rolling unit are relatively large, which is prone to accidents. Therefore, the thickness of the intermediate billet for SPA-C steel should be appropriately reduced, according to the different specifications of the finished product, the thickness of the intermediate billet for SPA-C steel is generally selected at 26-29mm. Immediately after the strip exits the finishing mill, it is water-cooled in an intensive manner, the cooling is accelerated in the front section, and the coiling temperature is controlled in the rear section, whose coiling temperature is (620±15)°C.