
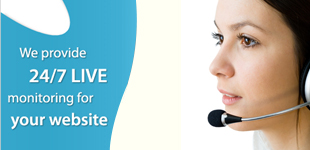
- : 0086-371-86151627 0086-371-86151827
- : 0086-371-86011881
- : [email protected]
- : [email protected]
- : bebonchina

- Boiler steels
- High carbon steel
- High Yield steel
- steel for welded tubes
- General construction steel
- steel with Cr.,Mo.,Cr-Mo
- Steel for large diameter pipes
- Simple pressure vessels steel
- Steel for gas cylinders and gas vessels
- General purpose structural steels
- Steel for boilers and pressure vessels
- steel resistant to atmospherical corrosion
- Carbon steel and low alloy steel
- Fine-grain structural steels,normalised rolled
- weldable normalized fine grained pressure vessel steels
The welding techniques of pressure vessel steel P355NH
The welding techniques of pressure vessel steel P355NH
P355NH steel is weldable fine-grain structural steel for pressure vessels, which is characterized by a minimum yield strength of 275-460 N/mm2.It is the unique mechanical properties that make P355NH steel possess good welding property.
The fine-grain structural steel grades of this series can be perfectly welded both manually and using automatic equipment by means of all known welding processes. However, the quality of the weld joint depends on the welding process, the welding conditions and the selection of the correct filler metals.
The welding wires and electrodes approved in this strength category must be used as filler metals. Basic coated elctrodes are recommended for manual welding.
In general, pre-heating prior to welding or torch-cutting is not necessary. At outside temperature below +5 °C, pre-heating to about 150 °C should be carried out.
Subsequent normalised or stress relief annealing with the grades rolled under normalised conditions is required only if called for in the regulations or if operating and manufacturing conditions make a reduction of the residual welding stresses appear useful. The thermo-mechanically rolled steels are not suitable for normalizing; stress relief annealing is possible. With stress relief annealing at 530–580 °C, the holding time should be 2 minutes per millimeter of plate thickness, not fall short of 30 minutes and not significantly exceed 60 minutes.
Excessively high annealing temperatures or excessively long annealing times bear the risk of reducing the strength values to below the condition of delivery.